Budowa maszyn pneumatycznych to dziedzina inżynierii zajmująca się projektowaniem oraz wytwarzaniem urządzeń wykorzystujących energię sprężonego powietrza do wykonywania różnych zadań. W maszynach pneumatycznych energia mechaniczna jest generowana przez sprężarki, które przekształcają energię elektryczną lub inną formę energii w energię sprężonego powietrza. To powietrze następnie przepływa przez system rur, zaworów i siłowników, co pozwala na wykonywanie pracy mechanicznej. Kluczowymi elementami budowy takich maszyn są sprężarki, zbiorniki ciśnieniowe, zawory sterujące oraz siłowniki pneumatyczne. Dzięki zastosowaniu technologii pneumatycznej możliwe jest uzyskanie dużej siły przy stosunkowo niskim zużyciu energii, co czyni te maszyny niezwykle efektywnymi w wielu branżach przemysłowych.
Jakie są główne komponenty budowy maszyn pneumatycznych?
W budowie maszyn pneumatycznych kluczowe znaczenie mają różnorodne komponenty, które współpracują ze sobą, aby zapewnić prawidłowe działanie całego systemu. Do najważniejszych elementów należą sprężarki, które odpowiadają za generowanie sprężonego powietrza. W zależności od zastosowania mogą to być sprężarki tłokowe, śrubowe lub membranowe. Kolejnym istotnym elementem są zbiorniki ciśnieniowe, które magazynują sprężone powietrze i zapewniają jego stabilny przepływ do pozostałych części systemu. Zawory sterujące umożliwiają kontrolowanie kierunku oraz ciśnienia powietrza w układzie, co jest niezbędne do precyzyjnego działania maszyn. Siłowniki pneumatyczne przekształcają energię sprężonego powietrza w ruch liniowy lub obrotowy, co pozwala na wykonywanie konkretnych zadań roboczych.
Jakie są zalety i wady budowy maszyn pneumatycznych?
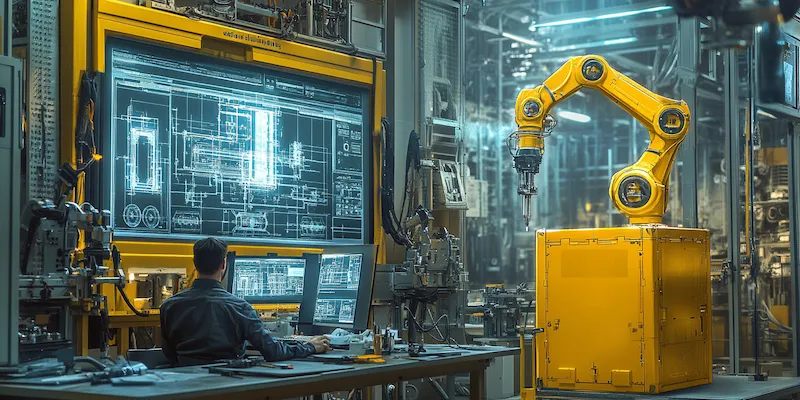
Budowa maszyn pneumatycznych wiąże się z wieloma zaletami oraz pewnymi ograniczeniami, które warto rozważyć przed podjęciem decyzji o ich zastosowaniu. Do głównych zalet należy zaliczyć dużą siłę roboczą przy niskim zużyciu energii, co sprawia, że maszyny te są niezwykle efektywne w wielu zastosowaniach przemysłowych. Ponadto maszyny pneumatyczne charakteryzują się prostotą konstrukcji oraz łatwością w serwisowaniu i naprawach, co obniża koszty eksploatacji. Dodatkowo ich działanie jest ciche i nie generuje dużych drgań, co wpływa na komfort pracy w zakładach produkcyjnych. Z drugiej strony istnieją również pewne wady związane z budową maszyn pneumatycznych. Przede wszystkim wymagają one dostępu do źródła sprężonego powietrza oraz odpowiedniej infrastruktury do jego transportu i przechowywania. Ponadto ich wydajność może być ograniczona przez straty ciśnienia w układzie oraz konieczność regularnej konserwacji elementów takich jak filtry czy zawory.
Jakie są zastosowania budowy maszyn pneumatycznych w przemyśle?
Zastosowania budowy maszyn pneumatycznych są niezwykle szerokie i obejmują wiele branż przemysłowych. W przemyśle motoryzacyjnym maszyny te wykorzystywane są do montażu komponentów oraz testowania części samochodowych dzięki swojej precyzyjnej kontroli ruchu. W branży spożywczej maszyny pneumatyczne znajdują zastosowanie przy pakowaniu produktów oraz transportowaniu surowców dzięki ich zdolności do pracy w warunkach higienicznych. W przemyśle elektronicznym wykorzystuje się je do montażu podzespołów elektronicznych oraz precyzyjnego lutowania. Również w branży budowlanej maszyny pneumatyczne odgrywają ważną rolę – używane są do narzędzi takich jak młoty pneumatyczne czy wiertnice, które ułatwiają wykonywanie prac budowlanych. Dodatkowo maszyny te znajdują zastosowanie w automatyce przemysłowej, gdzie służą do sterowania procesami produkcyjnymi i zwiększenia efektywności linii produkcyjnych.
Jakie są najnowsze technologie w budowie maszyn pneumatycznych?
W ostatnich latach rozwój technologii w dziedzinie budowy maszyn pneumatycznych przyspieszył, co zaowocowało wprowadzeniem innowacyjnych rozwiązań. Jednym z najważniejszych trendów jest automatyzacja procesów, która pozwala na zwiększenie wydajności i precyzji działania maszyn. Dzięki zastosowaniu nowoczesnych systemów sterowania, takich jak PLC (Programmable Logic Controller), możliwe jest zdalne monitorowanie oraz kontrolowanie pracy maszyn pneumatycznych. Kolejnym istotnym kierunkiem rozwoju jest integracja technologii IoT (Internet of Things), która umożliwia zbieranie danych o pracy maszyn oraz ich analizę w czasie rzeczywistym. To pozwala na szybsze wykrywanie usterek oraz optymalizację procesów produkcyjnych. Warto również zwrócić uwagę na rozwój materiałów używanych w budowie maszyn pneumatycznych, które stają się coraz lżejsze i bardziej wytrzymałe, co wpływa na ogólną efektywność i trwałość urządzeń.
Jakie są koszty związane z budową maszyn pneumatycznych?
Koszty związane z budową maszyn pneumatycznych mogą się znacznie różnić w zależności od wielu czynników, takich jak skomplikowanie projektu, rodzaj zastosowanych komponentów oraz wymagania dotyczące wydajności. Na początku warto uwzględnić koszty zakupu podstawowych elementów, takich jak sprężarki, zbiorniki ciśnieniowe, zawory czy siłowniki. Ceny tych komponentów mogą się różnić w zależności od producenta oraz specyfikacji technicznych. Dodatkowo należy brać pod uwagę koszty instalacji oraz uruchomienia systemu, które mogą obejmować prace związane z montażem oraz konfiguracją urządzeń. Warto również uwzględnić wydatki na konserwację oraz serwisowanie maszyn, które są niezbędne do zapewnienia ich długotrwałej i efektywnej pracy. Koszty eksploatacji mogą obejmować zużycie energii elektrycznej potrzebnej do pracy sprężarek oraz ewentualne koszty związane z wymianą filtrów czy innych elementów eksploatacyjnych.
Jakie są przyszłościowe kierunki rozwoju budowy maszyn pneumatycznych?
Przyszłość budowy maszyn pneumatycznych zapowiada się obiecująco, a wiele trendów wskazuje na dalszy rozwój tej technologii. Jednym z kluczowych kierunków jest dalsza automatyzacja procesów przemysłowych, co pozwoli na zwiększenie wydajności oraz redukcję kosztów produkcji. Integracja sztucznej inteligencji z systemami pneumatycznymi może przynieść nowe możliwości w zakresie analizy danych oraz optymalizacji procesów roboczych. Dzięki temu maszyny będą mogły samodzielnie dostosowywać swoje parametry do zmieniających się warunków produkcji. Kolejnym ważnym aspektem jest rozwój technologii bezprzewodowej komunikacji, co umożliwi łatwiejsze zarządzanie i monitorowanie pracy maszyn w czasie rzeczywistym. Wprowadzenie bardziej zaawansowanych materiałów kompozytowych do budowy komponentów pneumatycznych może przyczynić się do zwiększenia ich trwałości oraz zmniejszenia wagi, co wpłynie na ogólną efektywność systemu.
Jakie są wyzwania związane z budową maszyn pneumatycznych?
Budowa maszyn pneumatycznych wiąże się z wieloma wyzwaniami, które inżynierowie i projektanci muszą brać pod uwagę podczas tworzenia nowych rozwiązań. Jednym z głównych problemów jest konieczność zapewnienia odpowiedniej jakości sprężonego powietrza, które ma kluczowe znaczenie dla prawidłowego funkcjonowania całego systemu. Zanieczyszczenia czy wilgoć mogą prowadzić do uszkodzeń komponentów oraz obniżenia wydajności maszyn. Dlatego tak ważne jest stosowanie odpowiednich filtrów i osuszaczy powietrza. Kolejnym wyzwaniem jest optymalizacja układów pneumatycznych pod kątem minimalizacji strat ciśnienia, co ma bezpośredni wpływ na efektywność energetyczną systemu. Warto również zwrócić uwagę na konieczność regularnego serwisowania i konserwacji urządzeń, aby zapewnić ich długotrwałą i niezawodną pracę.
Jakie są różnice między maszynami pneumatycznymi a hydraulicznymi?
Maszyny pneumatyczne i hydrauliczne to dwa różne typy urządzeń wykorzystywanych w przemyśle do wykonywania pracy mechanicznej, jednak różnią się one zasadniczo pod względem działania oraz zastosowanych mediów roboczych. Maszyny pneumatyczne wykorzystują sprężone powietrze jako medium robocze, co sprawia, że są lżejsze i prostsze w konstrukcji niż maszyny hydrauliczne, które operują cieczą pod wysokim ciśnieniem. Dzięki temu maszyny pneumatyczne charakteryzują się mniejszymi wymaganiami dotyczącymi infrastruktury oraz łatwiejszym serwisowaniem. Z drugiej strony maszyny hydrauliczne oferują znacznie większą siłę roboczą przy mniejszych gabarytach urządzeń, co czyni je bardziej odpowiednimi do zastosowań wymagających dużych obciążeń lub precyzyjnego sterowania ruchem. Wybór między tymi dwoma typami maszyn zależy od specyfiki danego zadania oraz wymagań dotyczących wydajności i efektywności energetycznej procesu produkcyjnego.
Jakie są przykłady zastosowania budowy maszyn pneumatycznych w codziennym życiu?
Budowa maszyn pneumatycznych znajduje zastosowanie nie tylko w przemyśle, ale także w codziennym życiu, gdzie ułatwiają wiele rutynowych czynności. Przykładem mogą być narzędzia pneumatyczne używane przez majsterkowiczów i profesjonalistów – takie jak pistolety do malowania czy klucze udarowe – które dzięki swojej wydajności pozwalają na szybkie wykonanie prac remontowych czy budowlanych. W branży spożywczej maszyny pneumatyczne są wykorzystywane do pakowania produktów spożywczych oraz transportu surowców między poszczególnymi etapami produkcji. Również w medycynie znajdują zastosowanie urządzenia oparte na technologii pneumatycznej – przykładem mogą być aparaty do rehabilitacji czy sprzęt chirurgiczny wspomagany sprężonym powietrzem. Maszyny te można spotkać także w systemach klimatyzacyjnych czy wentylacyjnych w domach i biurach, gdzie odpowiadają za cyrkulację powietrza i utrzymanie odpowiednich warunków atmosferycznych we wnętrzu budynków.