Smarowanie narzędzi pneumatycznych jest kluczowym elementem ich konserwacji, który wpływa na wydajność oraz trwałość urządzeń. Aby skutecznie smarować narzędzia pneumatyczne, należy najpierw zrozumieć, jakie rodzaje smarów są odpowiednie do danego typu narzędzia. W przypadku narzędzi pneumatycznych najczęściej stosuje się oleje na bazie mineralnej lub syntetycznej, które zapewniają odpowiednią lepkość i właściwości smarne. Ważne jest również, aby stosować smary zalecane przez producenta narzędzi, ponieważ różne modele mogą wymagać różnych specyfikacji. Proces smarowania powinien być przeprowadzany regularnie, zwłaszcza po intensywnym użytkowaniu narzędzi. Należy pamiętać o czyszczeniu narzędzi przed nałożeniem smaru, aby usunąć wszelkie zanieczyszczenia, które mogą wpłynąć na działanie mechanizmu. Dobrą praktyką jest również sprawdzenie poziomu smaru w zbiorniku narzędzia przed każdym użyciem, co pozwoli uniknąć problemów związanych z niewystarczającą ilością oleju w systemie.
Jakie są najlepsze techniki smarowania narzędzi pneumatycznych?
Właściwe techniki smarowania narzędzi pneumatycznych mają kluczowe znaczenie dla ich efektywności i długowieczności. Jedną z najpopularniejszych metod jest smarowanie poprzez system automatycznego podawania oleju, który dostarcza odpowiednią ilość smaru do narzędzia w trakcie jego pracy. Tego rodzaju rozwiązania są szczególnie przydatne w przypadku intensywnego użytkowania narzędzi w przemyśle, gdzie regularne przerywanie pracy w celu manualnego smarowania byłoby nieefektywne. Inną metodą jest ręczne smarowanie, które polega na aplikacji oleju bezpośrednio na ruchome części narzędzia za pomocą pędzelka lub strzykawki. Ważne jest, aby nie przesadzić z ilością smaru, ponieważ nadmiar może prowadzić do gromadzenia się zanieczyszczeń i obniżenia wydajności urządzenia. Warto także zwrócić uwagę na to, aby stosować odpowiednie akcesoria do smarowania, takie jak filtry powietrza czy separatory wody, które pomogą utrzymać czystość systemu pneumatycznego i zapobiegną uszkodzeniom spowodowanym przez zanieczyszczenia.
Jak często należy smarować narzędzia pneumatyczne dla optymalnej wydajności?
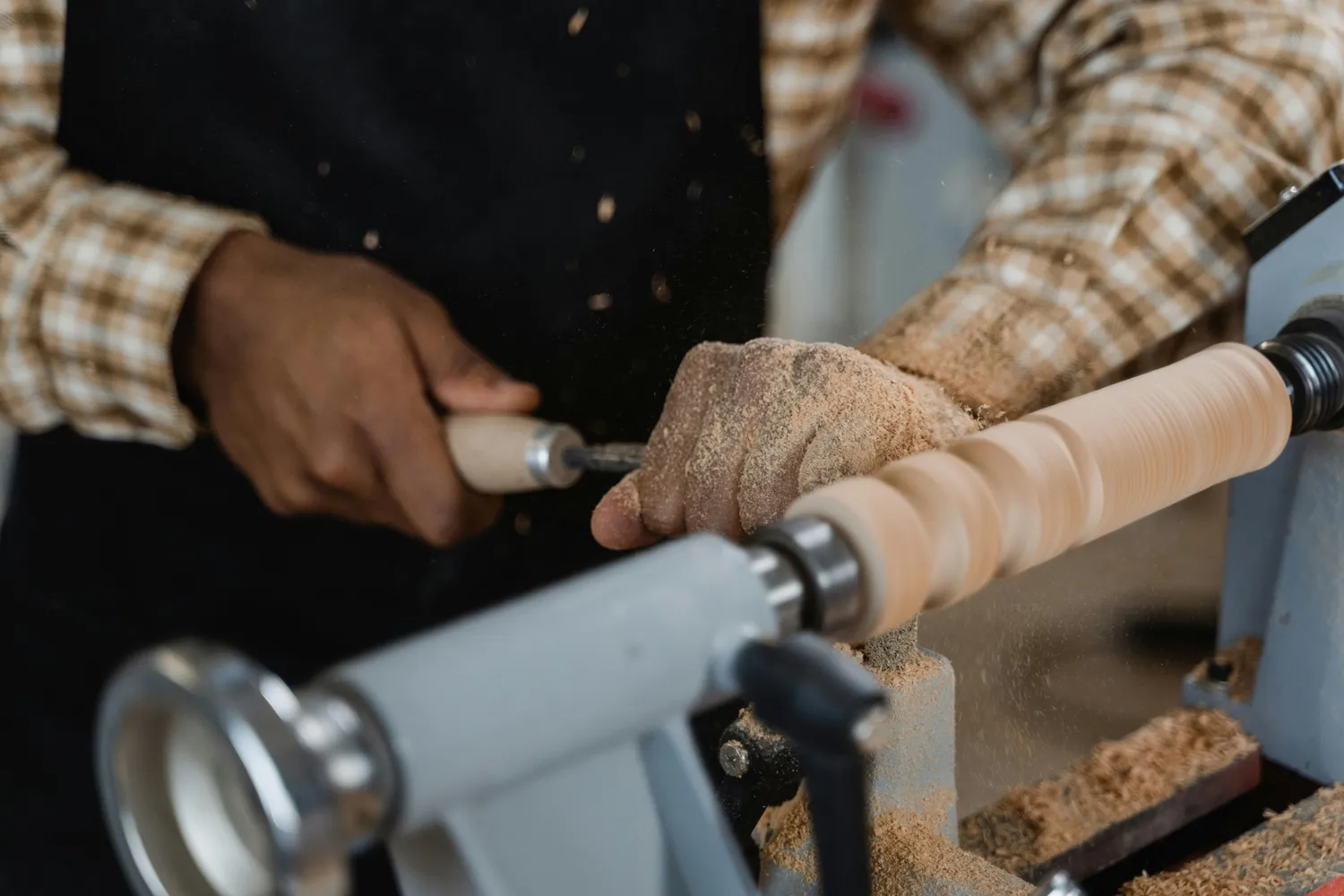
Określenie częstotliwości smarowania narzędzi pneumatycznych zależy od wielu czynników, takich jak intensywność użytkowania, warunki pracy oraz specyfika samego narzędzia. W przypadku standardowego użytkowania zaleca się przeprowadzanie procesu smarowania co 8 godzin pracy lub po każdej zmianie roboczej. W sytuacjach intensywnego użytkowania lub w trudnych warunkach środowiskowych, takich jak wysoka wilgotność czy obecność pyłów przemysłowych, warto rozważyć częstsze smarowanie co 4 godziny lub nawet co 2 godziny. Dobrą praktyką jest również obserwacja działania narzędzi – jeśli zaczynają one wydawać niepokojące dźwięki lub zauważalne jest zmniejszenie ich wydajności, może to być sygnałem do natychmiastowego przeprowadzenia smarowania. Nie należy również zapominać o regularnym sprawdzaniu poziomu oleju w zbiorniku oraz wymianie filtrów powietrza, co ma kluczowe znaczenie dla prawidłowego funkcjonowania systemu pneumatycznego.
Jakie są skutki niewłaściwego smarowania narzędzi pneumatycznych?
Niewłaściwe smarowanie narzędzi pneumatycznych może prowadzić do szeregu negatywnych konsekwencji zarówno dla samego urządzenia, jak i dla jakości wykonywanej pracy. Jednym z najczęstszych skutków jest zwiększone zużycie elementów ruchomych, co może prowadzić do ich szybszego uszkodzenia i konieczności kosztownej naprawy lub wymiany. Brak odpowiedniej ilości smaru powoduje tarcie między ruchomymi częściami, co przekłada się na obniżenie efektywności działania narzędzia oraz wzrost zużycia energii potrzebnej do jego obsługi. Z kolei nadmiar oleju może prowadzić do gromadzenia się zanieczyszczeń i powstawania osadów wewnątrz mechanizmu, co również negatywnie wpływa na jego funkcjonowanie. Ponadto niewłaściwe smarowanie może skutkować zwiększeniem hałasu podczas pracy urządzenia oraz obniżeniem precyzji wykonywanych zadań. W skrajnych przypadkach brak odpowiedniej konserwacji może doprowadzić do całkowitego uszkodzenia narzędzia i konieczności jego wymiany.
Jakie narzędzia i akcesoria są potrzebne do smarowania narzędzi pneumatycznych?
Aby skutecznie smarować narzędzia pneumatyczne, warto zaopatrzyć się w odpowiednie narzędzia i akcesoria, które ułatwią ten proces. Podstawowym elementem wyposażenia jest olej do narzędzi pneumatycznych, który powinien być dostosowany do specyfikacji producenta. Warto wybierać oleje o odpowiedniej lepkości, które zapewnią optymalne smarowanie oraz ochronę przed zużyciem. Kolejnym istotnym akcesorium jest smarownica, która umożliwia precyzyjne dozowanie oleju na ruchome części narzędzia. Smarownice mogą mieć różne formy, od prostych ręcznych po bardziej zaawansowane modele automatyczne, które zapewniają stałe podawanie smaru podczas pracy. Dodatkowo przydatne mogą być filtry powietrza oraz separatory wody, które pomagają w utrzymaniu czystości systemu pneumatycznego i zapobiegają zanieczyszczeniu oleju. Nie można zapomnieć o ściereczkach i materiałach do czyszczenia, które pozwolą na usunięcie zanieczyszczeń przed nałożeniem nowego smaru. Warto również mieć pod ręką szczotki i narzędzia do demontażu, które mogą być potrzebne w przypadku bardziej skomplikowanej konserwacji narzędzi.
Jakie są najczęstsze błędy podczas smarowania narzędzi pneumatycznych?
Podczas smarowania narzędzi pneumatycznych można popełnić wiele błędów, które mogą negatywnie wpłynąć na ich funkcjonowanie oraz trwałość. Jednym z najczęstszych błędów jest stosowanie niewłaściwego rodzaju oleju, co może prowadzić do uszkodzenia mechanizmów wewnętrznych. Ważne jest, aby zawsze korzystać z olejów zalecanych przez producenta narzędzi, ponieważ różne modele mogą wymagać różnych specyfikacji. Innym powszechnym błędem jest nadmierna ilość smaru, co może prowadzić do gromadzenia się zanieczyszczeń oraz osadów wewnątrz urządzenia. Zbyt duża ilość oleju może również powodować wycieki i zanieczyszczenie miejsca pracy. Niezbyt częste smarowanie to kolejny problem, który może prowadzić do szybszego zużycia elementów ruchomych oraz obniżenia wydajności narzędzia. Warto także pamiętać o konieczności czyszczenia narzędzi przed nałożeniem nowego smaru, ponieważ resztki starego oleju oraz zanieczyszczenia mogą wpłynąć na jakość smarowania. Wreszcie, niektóre osoby zapominają o regularnym sprawdzaniu poziomu oleju w zbiorniku lub nie zwracają uwagi na oznaki zużycia narzędzi, co może prowadzić do poważnych problemów w przyszłości.
Jakie są korzyści płynące z regularnego smarowania narzędzi pneumatycznych?
Regularne smarowanie narzędzi pneumatycznych przynosi szereg korzyści, które mają kluczowe znaczenie dla ich wydajności oraz trwałości. Przede wszystkim odpowiednie smarowanie zmniejsza tarcie między ruchomymi częściami urządzenia, co przekłada się na zwiększenie efektywności działania narzędzia oraz mniejsze zużycie energii. Dzięki temu praca staje się bardziej wydajna, a czas potrzebny na wykonanie zadania ulega skróceniu. Regularne smarowanie wpływa również na dłuższą żywotność narzędzi – dobrze nasmarowane mechanizmy są mniej podatne na uszkodzenia i awarie, co pozwala uniknąć kosztownych napraw lub wymiany sprzętu. Dodatkowo odpowiednia konserwacja wpływa na jakość wykonywanej pracy – dobrze działające narzędzie zapewnia lepszą precyzję i dokładność podczas realizacji zadań. Regularne smarowanie pomaga także w utrzymaniu czystości systemu pneumatycznego poprzez eliminację zanieczyszczeń i osadów, co ma kluczowe znaczenie dla prawidłowego funkcjonowania całego układu.
Jakie są różnice między smarowaniem manualnym a automatycznym?
Smarowanie manualne i automatyczne to dwie różne metody konserwacji narzędzi pneumatycznych, każda z nich ma swoje zalety i ograniczenia. Smarowanie manualne polega na ręcznym aplikowaniu oleju na ruchome części narzędzia za pomocą pędzelka lub strzykawki. Ta metoda daje użytkownikowi pełną kontrolę nad ilością używanego smaru oraz miejscem jego aplikacji, co może być korzystne w przypadku precyzyjnych prac wymagających szczególnej uwagi. Jednakże wymaga ona więcej czasu i wysiłku ze strony operatora oraz może prowadzić do pominięcia niektórych elementów podczas konserwacji. Z kolei smarowanie automatyczne opiera się na systemach podawania oleju, które dostarczają odpowiednią ilość smaru do urządzenia podczas jego pracy. Tego rodzaju rozwiązania są szczególnie przydatne w intensywnym użytkowaniu przemysłowym, gdzie regularne przerywanie pracy byłoby nieefektywne. Automatyczne systemy smarowania zapewniają równomierne rozprowadzenie oleju oraz minimalizują ryzyko pominięcia ważnych elementów mechanizmu. Mimo to mogą być droższe w instalacji i wymagają regularnej konserwacji samego systemu podawania oleju.
Jakie są najlepsze praktyki dotyczące przechowywania narzędzi pneumatycznych?
Prawidłowe przechowywanie narzędzi pneumatycznych ma kluczowe znaczenie dla ich długowieczności oraz niezawodności działania. Narzędzia powinny być przechowywane w suchym i czystym miejscu, aby uniknąć korozji oraz gromadzenia się zanieczyszczeń. Warto zadbać o odpowiednie opakowania lub stojaki do przechowywania narzędzi, które zabezpieczą je przed uszkodzeniami mechanicznymi oraz przypadkowymi upadkami. Ponadto przed dłuższym okresem przechowywania warto dokładnie oczyścić urządzenia z resztek oleju oraz innych zanieczyszczeń, a także nałożyć cienką warstwę ochronnego smaru na metalowe części, aby zapobiec korozji. Należy również pamiętać o regularnym sprawdzaniu stanu technicznego przechowywanych narzędzi – należy zwrócić uwagę na ewentualne oznaki zużycia czy uszkodzeń mechanicznych i podejmować odpowiednie kroki naprawcze przed ponownym użyciem sprzętu.